Le duromètre Rockwell mesure la résistance d’un objet à la déformation plastique sous une charge définie et à un taux de charge spécifié, mesurée en unités appelées dynes par millimètre carré.
La norme utilisée pour mesurer cette propriété est l’ASTM D-3574. Elle a été développée par le Dr William H.F. Rockwell en 1938. Un instrument typique se compose de deux plateaux parallèles qui sont chargés avec une force croissante jusqu’à ce qu’ils se touchent ; lorsque cela se produit, la pression augmente linéairement jusqu’à une valeur maximale fixée manuellement ou par ordinateur.
À tout moment pendant l’essai, la distance entre les extrémités du plateau peut être lue sur des cadrans calibrés. Cela donne une mesure de la force nécessaire pour presser l’échantillon dans la plasticité.
Instrumentation :
Une méthode courante pour déterminer la dureté des matériaux consiste à utiliser un appareil d’essai de dureté tel que l’appareil d’essai de dureté Rockwell. En outre, il existe de nombreux types d’instruments différents disponibles auprès de divers fabricants qui déterminent la dureté des matériaux. Il s’agit notamment de :
Méthode d’essai duromètre Rockwell un indenteur est placé contre la surface de l’échantillon. Lorsque le pénétrateur entre en contact avec la surface, la force appliquée provoque une déformation élastique de la surface autour du point de contact. Dès que le pénétrateur quitte la surface, la reprise élastique se produit immédiatement.
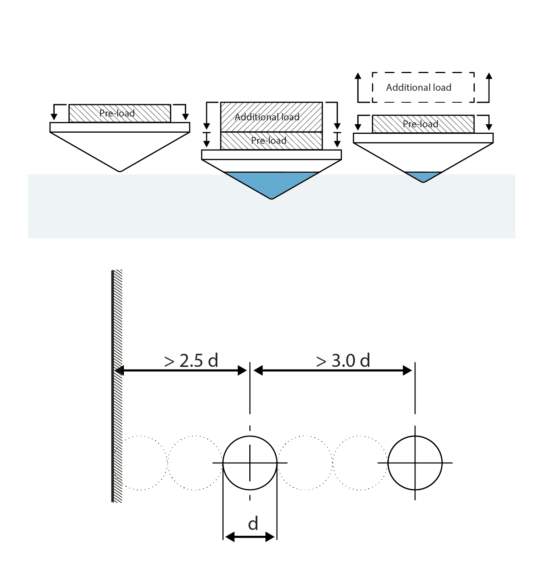
L’énergie totale requise pour provoquer ces événements est enregistrée comme le nombre de « dureté ». Les essais d’indentation ont été largement utilisés pour caractériser les propriétés mécaniques des matériaux. Les indentations peuvent être réalisées manuellement ou automatiquement.
Les méthodes manuelles consistent à placer le pénétrateur sur la surface testée, puis à appuyer suffisamment fort pour que la pointe pénètre légèrement sous la surface. Après avoir retiré le pénétrateur, on note la profondeur de pénétration. Les techniques automatiques utilisent une machine capable de déplacer le pénétrateur sur la surface testée tout en enregistrant sa position et son mouvement.
La mesure de la dureté est devenue importante grâce aux nouvelles technologies :
Par exemple, l’usinage à grande vitesse exige des outils de coupe très durs ; les composites renforcés de fibres de verre nécessitent des fibres à module élevé ; les céramiques doivent être plus résistantes que les métaux classiques, etc.
Il existe plusieurs façons d’obtenir des données sur la microstructure d’une pièce composite. L’une d’elles consiste à découper de petits échantillons de la pièce et à les soumettre à un examen microscopique. Une autre approche utilise l’analyse par diffraction des rayons X. Une autre technique encore consiste à réaliser une série de coupes transversales de la pièce et à analyser leurs microstructures.
Ces trois approches fournissent des informations sur la distribution des phases au sein de la matrice et révèlent également des détails concernant la taille et l’orientation des grains. Cependant, ces trois méthodes présentent certains inconvénients. Le découpage ne produit que des quantités limitées de matériau représentatif. La coupe transversale détruit la structure originale. Et la diffractométrie des rayons X ne donne pas un accès direct aux distributions de phase.